Process Optimisation Regarding Overall Equipment Effectiveness of Tyre Manufacturing using Response Surface Methodology and Grey Relational Analysis
doi: 10.14456/mijet.2021.17
Keywords:
Benchmarking, optimisation, tyre manufacturing, response surfaceAbstract
This paper presents a response surface methodology optimisation approach using the central composite design and the grey relational analysis to optimise the overall equipment effectiveness (OEE) for the tyre manufacturing process. In this paper, a parametric analysis based on availability, performance rate and the quality rate is conducted for a tyre manufacturing process using experimental data obtained from the literature. The outcome of the study supports the optimisation of OEE using the methods and establishes that they are effective. This may serve as a beneficial reference for the periodic operation of the tyre plant and could be effectively applied to detect variance of the OEE component factors during actual operation by referring to the predictions. This paper could be valuable for tyre manufacturing professionals engaged in the production of tyres in the development process. The work helps tyre manufacturers to improve on their substantial weakness in operations and engineering management.
References
Ahire C.P., Relkar A.S., 2012, Correlating failure mode effect analysis (FMEA) & overall equipment effectiveness (OEE), Procedia Engineering, Vol 38, pp. 3482-3486.
Baghbani M., Iranzadeh S., Khajeh M.B., 2019, Investigating the relationship between RPN parameters in fuzzy PFMEA and OEE in a sugar factory, Journal of Loss Prevention in the Process Industries, Vol 60, pp. 221-232.
Becker J.M.J., Borst J., der Veen A., 2015, Improving the overall equipment effectiveness in high-mix-low-volume manufacturing environments, CIRP Annals, Vol. 64, No. 1, pp. 419-422
Braglia M., Castellano D., Frosolini M., Gallo M., 2019, Integrating considerations of uncertainty within the OEE of a manufacturing line, International Journal of Industrial and Systems Engineering, Vol.32 No.4, pp.469-496. DOI: 10.1504/IJISE.2019.10010483
Cesarotti V., Introna V., Rotunno R., Scerrato G., 2016, Investigating the relationship between energy consumption and overall equipment effectiveness for improving manufacturing systems' productivity: an application in the thermoforming process, International Journal of Productivity and Quality Management, Vol.18 No.2/3, pp.279-300. DOI: 10.1504/IJPQM.2016.076711
Chiarini A. 2015, Improvement of OEE performance using a Lean Six Sigma approach: an Italian manufacturing case study, International Journal of Productivity and Quality Management, Vol.16 No.4, pp.416-433. DOI: 10.1504/IJPQM.2015.072414
Chikwendu O.C., Chima A.S., Edith M.C., 2020, The optimization of overall equipment effectiveness factors in a pharmaceutical company, Heliyon, Vol. 6, e03796, pp. 1-9
Chittilla K., Yeola Y., Tiwari A., and Rajamanickam R., 2013, Effect of excitation methods on experimental modal analysis of passenger car tire, SAE Technical Papers, Vol. 12, Article ID 2013-01-2854, 5 pages
Deng, J. L., 1989. Introduction to grey system theory. The Journal of Grey System, Vol. 1, pp. 1–24.
Fauzi A., and Doloksaribu G., 2016, Efforts in improving overall equipment effectiveness of weaving machine in tyre cord division at tyre manufacturing company in Indonesia, International Journal of Science and Research, Vol. 5, No. 7, pp. 730-735
Godfrey S.J., Murugan S.S., 2018, Stability control of vehicles during tyre burst with auto expanding rims, Journal of Automation and Automobile Engineering Vol. 3, No. 2, pp. 1-5
Gupta V., Jain R., Meena M. L. and Dangayach G.S., 2018, Six-sigma application in tire-manufacturing company: a case study. Journal of Industrial Engineering International, Vol. 14, pp. 511–520. https://doi.org/10.1007/s40092-017-0234-6
Guolin W. and Jianjun W., 2012. Rolling resistance finite element analysis of radial truck tyre, Computer Simulation, Vol. 28, No. 11, pp. 332–334.
Hanumantharaya R., Sogalad I., Basavarajappa S., Patel G.C.M. 2019, Modelling and optimisation of adhesive bonded joint strength of composites for aerospace applications, International Journal of Computational Materials Science and Surface Engineering, Vol.8 No. 3/4, pp.167-184. DOI: 10.1504/IJCMSSE.2019.104694
Heng Z., Aiping L., Liyun X., Moroni G., 2019, Automatic Estimate of OEE Considering Uncertainty, Procedia CIRP, Vol 81, pp. 630-635.
Hedman R., Subramaniyan M., Almstrom P., 2016, Analysis of critical factors for automatic measurement of OEE, Procedia CIRP, Vol 57, pp.128-133.
Hsu Y.L., Li W.C., Chen K.W., 2010. Structuring critical success factors of airline safety management system using a hybrid model, Transportation Research Part E, vol. 46, pp. 222–235.
Javanmarch E and Liu S., 2019, exploring grey systems theory-based methods and applications in analyzing socio-economic systems, sustainability, Vol. 11, Article 4192, 1-19.
Jasiulewicz-Kaczmarek M.G. and Piechowski M., 2016, Practical aspects of OEE in automotive company – case study, International Conference on Management Science and Management Innovation, pp. 213-218. doi:10.2991/msmi-16.2016.51
Khuri A.I., 2017), A general overview of response surface methodology, Biometrics and Biostatistics International Journal, Vol.5, No.3, pp.87-93
Kigsirisin S., Pussawiro S., Noohawm O., 2016, Approach for total productive maintenance evaluation in water productivity: a case study at Mahasawat water treatment plant, Procedia Engineering, Vol 154, pp. 260-267.
Kole P.J., Löhr A.J., Van Belleghem F.G. and Ragas A.M.J. 2017, Wear and tear of tyres: A stealthy source of microplastics in the environment, International Journal of Environmental Research and Public Health, Vol. 14, No. 10, 1265, https://doi.org/10.3390/ijerph14101265
Krishnan S., Dev A.S., Suresh R., Sumesh A., Rameshkumar K., 2018, Bottleneck identification in a tyre manufacturing plant using simulation analysis and productivity improvement, Materials Today: Proceedings, Vol. 5, No. 11, pp. 24720-24730, https://doi.org/10.1016/j.matpr.2018.10.270
Lebreton B., Tuma A. 2006, A quantitative approach to assessing the profitability of car and truck tire remanufacturing, International Journal of Production Economics, Vol. 104, No. 2, pp. 639-652. DOI: 10.1016/j.ijpe.2004.11.010
Li B., Bei S. and Zhao J., 2017, Research method of tyre contact characteristics based on modal analysis, Mathematical Problems in Engineering, Volume 2017, Article ID 6769387, https://doi.org/10.1155/2017/6769387
Manjaiah M., Deenashree K.N., Basavarajappa S., 2019, WED-machining characteristics of Ti6Al4V alloy based on central composite design, International Journal of Materials and Product Technology, Vol.59 No.2, pp.121–139. DOI: 10.1504/IJMPT.2019.102634
Mâinea M., Duţă L., Patic P.C., Căciulă I., 2010, A method to optimize the overall equipment effectiveness, IFAC Proceedings Volumes, Vol. 43, No. 17, pp. 237-241
Mele C., Pels J., Polese F. 2010, A brief review of systems theories and their managerial applications, Service Science, Vol. 2, pp. 126-135.
Mehdiabadi A., Amirabdollahian S., Rohani A., Farahani N.M., 2013, Qualitative-quantitative analysis of tire industry of Iran by using fuzzy DEMATEL and systemic method until 1404, International Journal of Scientific & Engineering Research, Vol. 4, No. 9, pp. 1939-1946
Offor I.F., Ehiri R.C., Ude C.O., 2015, Factors interactions and the modelling of biodiesel production from Jatropha curcas oil, International Journal of Renewable Energy Technology, Vol.6 No.2, pp.181–195. DOI: 10.1504/IJRET.2015.068597
Onyegiri I.E. and Oke S.A., 2017. A grey relational analytical approach to safety performance assessment in an aviation industry in the developing country, Engineering and Applied Science Research, Vol. 44, No. 1, pp. 1-15.
Rao G.S., Rao A.N. 2012, Comparison of central composite and orthogonal array designs for cutting force and surface roughness prediction modelling in turning, International Journal of Materials and Product Technology, Vol.43 No.1/2/3/4, pp.144–164. DOI: 10.1504/IJMPT.2012.047641
Rita G., Luca G., Francesco L., Bianca R., 2017, On the analysis of effectiveness in a manufacturing cell: A critical implementation of existing approaches, Procedia Manufacturing, Vol 11, pp.1882-1891.
Ranteshwar S., Shah D.B., Gohil A.M., Shah M.H., 2013, Overall equipment effectiveness (OEE) calculation – automation through hardware & software development, Procedia Engineering. Vol 51, pp. 579-584.
Raja P.N., 2008, Strategic OEE models for assessing real effectiveness to improve deployment of manufacturing resources, Ph.D. Thesis, Faculty of Mechanical Engineering, Anna University, Chennai, India
Raji A.O. and Oke S.A., 2019, Enhancement of maintenance downtime using Poisson motivated-Taguchi optimisation method, Al-Nahrain Journal for Engineering Sciences, Vol. 22, No. 4, pp. 294-306.
Relkar A.S., Nandurkar K.N., 2012, Optimizing & analysing overall equipment effectiveness (OEE) through design of experiments (DOE), Procedia Engineering, Vol 38, pp. 2973-2980.
Rui O., Taki S.A., Sousa S., Salimi M.A., 2019, Global process effectiveness: When overall equipment effectiveness meets adherence to schedule, Procedia Manufacturing, Vol 38, pp. 1615-1622.
Roessler M.P., Abele E., 2015, Enhancement of the overall equipment effectiveness measure: a contribution for handling uncertainty in shop floor optimisation and production planning, International Journal of Industrial and Systems Engineering, Vol.20 No.2, pp.141-154. DOI: 10.1504/IJISE.2015.069545
Shahin A., Isfahani N.G., 2015, Estimating overall equipment effectiveness for continuous production lines: with a case study in Esfahan Steel Company, International Journal of Services and Operations Management, Vol.21 No.4, pp.466 - 478. DOI: 10.1504/IJSOM.2015.070252
Sharma R., 2019, Overall equipment effectiveness measurement of TPM manager model machines in flexible manufacturing environment: a case study of automobile sector, 2019, International Journal of Productivity and Quality Management, Vol.26 No.2, pp.206 - 222, DOI: 10.1504/IJPQM.2019.097767
Singh R.K., Clements E., Sonwaney V., 2018, Measurement of overall equipment effectiveness to improve operational efficiency, International Journal of Process Management and Benchmarking, Vol.8 No.2, pp.246 - 261. DOI: 10.1504/IJPMB.2018.090798
Saleem F., Nisar S., Khan M., Khan S.Z., Sheikh M.A., 2017, Overall equipment effectiveness of tyre curing press: A case study, Journal of Quality in Manufacturing Engineering, Vol. 23, No. 1, pp. 39-56, doi: 10.1108/jqme-06-2015-0021
Simsek B., Ic Y.T., 2014, Multi-response simulation optimization approach for the performance optimization of an alarm monitoring center, Safety Science, Vol. 66, pp. 61–74
Santos J., Munoz-Villamizar A., Montoya-Torres J.R., Jaca C., 2018, Using OEE to evaluate the effectiveness of urban freight transportation systems: A case study, International Journal of Production Economics, Vol 197, pp. 232-242.
Tantanawat T., Puckdeesorasuk N., Haewchin A., Viyanit E., 2018, The application of overall equipment effectiveness to support the development of a steamless nut-separated palm oil mill, International Journal of Process Management and Benchmarking, Vol.8 No.2, pp. 206-227. DOI: 10.1504/IJPMB.2018.090797
Tsarouhas, P., 2019, Overall equipment effectiveness (OEE) evaluation for an automated ice cream production line: A case study, International Journal of Productivity and Performance Management, Vol. 69 No. 5, pp. 1009-1032. https://doi.org/10.1108/IJPPM-03-2019-0126
Vivekprabhu M., Karthick R., Senthilkumar G., 2014, Optimisation of overall equipment effectiveness in a manufacturing system, International Journal of Innovative Research in Science, Engineering and Technology, Vol.3, No. 3, pp. 1192-1196
Vigneshkumar M., Varthanan P.A., 2019, Comparison of RSM and ANN model in the prediction of the tensile shear failure load of spot welded AISI 304/316 L dissimilar sheets, International Journal of Computational Materials Science and Surface Engineering, Vol.8 No.2, pp.114–130. DOI: 10.1504/IJCMSSE.2019.102292
Yuniawan D., Ito T., Mohamad E.B., 2014, Overall equipment effectiveness estimation for priority improvement in the production line, International Journal of Internet Manufacturing and Services, 2014 Vol. 3 No. 4, pp. 279 - 299. DOI: 10.1504/IJIMS.2014.070694
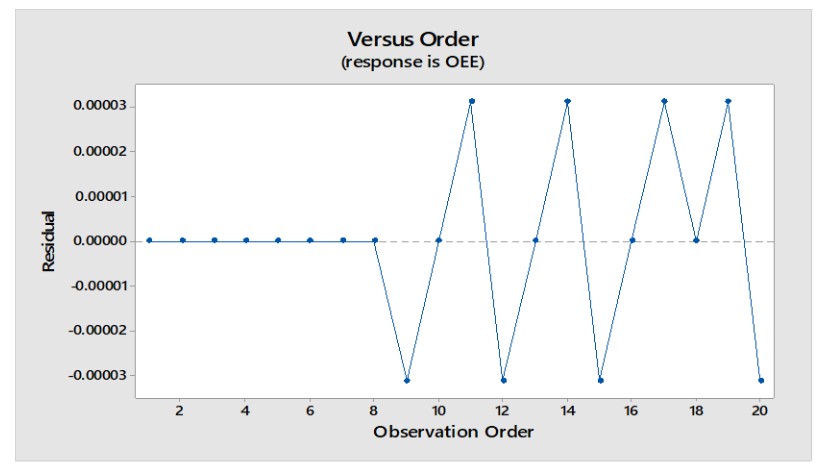
Downloads
Published
How to Cite
Issue
Section
License
Copyright (c) 2021 Engineering Access

This work is licensed under a Creative Commons Attribution-NonCommercial-NoDerivatives 4.0 International License.