Improving Overall Equipment Effectiveness of the Plaster Mold Process using Lean Manufacturing Principles
doi: 10.14456/mijet.2023.17
Keywords:
Overall equipment effectiveness, availability rate, performance rate, quality rate, plaster moldAbstract
The purpose of this research was to improve the production process for plaster molds by utilizing overall equipment effectiveness (OEE). Data collected prior to the improvement revealed low performance due to lost time during preparation, movement, and waiting. Lean tools such as work studies, flow process charts, and man-machine charts were used to identify the root causes of these issues. The issues can be categorized using seven waste principles, including transportation and walking that is excessive. Defects occurred during the process. A machine idles occurred during the process. There was too much worker motion in the process. An extra-process was taken because the defective parts had to be repaired. Improvements were made using lean manufacturing, separating internal and external work, and ECRS principles, resulting in an increase in performance rate from 42.27% to 90.34%, an increase in overall equipment effectiveness from 38.18% to 81.56%, and a 25% decrease in the number of workers from 8 to 6. The labor productivity rate increased from 0.140 to 0.145 set per person per hour. Improved overall equipment effectiveness leads to increased process efficiency and productivity. As a result, it is one of the most effective tools for process improvement.
References
A. Yaghoubi, S. Rahimi, R. Soltani, and S. T. A. Niaki, “Availability analysis of a cooking oil production line,” J. Optim. Ind. Eng., vol. 14, no. 1, pp. 1–9, 2021, doi: 10.22094/joie.2020.1889992.1712.
T. Haddad, B. W. Shaheen, and I. Németh, “Improving Overall Equipment Effectiveness (OEE) of Extrusion Machine Using Lean Manufacturing Approach,” Manuf. Technol., vol. 21, no. 1, pp. 56–64, 2021, doi: 10.21062/mft.2021.006.
M. Suryaprakash, M. Gomathi Prabha, M. Yuvaraja, and R. V. Rishi Revanth, “Improvement of overall equipment effectiveness of machining centre using tpm,” Mater. Today Proc., vol. 46, no. xxxx, pp. 9348–9353, 2019, doi: 10.1016/j.matpr.2020.02.820.
A. Palange and P. Dhatrak, “Lean manufacturing a vital tool to enhance productivity in manufacturing,” Mater. Today Proc., vol. 46, pp. 729–736, 2021, doi: 10.1016/j.matpr.2020.12.193.
R. K. Kennedy, Understanding, Measuring, and Improving Overall Equipment Effectiveness. 2017. doi: 10.4324/9781315166957.
S. Bhade and S. Hegde, “Improvement of Overall Equipment Efficiency of Machine by SMED,” Mater. Today Proc., vol. 24, pp. 463–472, 2020, doi: 10.1016/j.matpr.2020.04.298.
J. K. Liker, The Toyota Way: 14 Management Principles from the World’s Greatest Manufacturer, 1st ed. McGraw-Hill, 2003.
J. P. Womack and D. T. Jones, Lean Thinking: Banish Waste and Create Wealth in Your Corporation, 2nd ed. Free Press, 2003. doi: 10.1007/BF01807056.
N. Sriputtha and B. Nadondu, “Wastes Reduction in Turning Process of Pipe Joint by Using ECRS Technique,” in the 11th Rajamangala University of Technology National Conference, 2019, pp. 605–616.
S. Basak, M. Baumers, M. Holweg, R. Hague, and C. Tuck, “Reducing production losses in additive manufacturing using overall equipment effectiveness,” Addit. Manuf., vol. 56, no. May, p. 102904, 2022, doi: 10.1016/j.addma.2022.102904.
T. H. Lakho, M. A. Khan, S. I. Virk, A. A. Indher, and S. A. Khaskheli, “Evaluation of Overall Equipment Effectiveness in a Heavy Engineering Industry: A Case Study,” in Proceedings of the International Conference on Industrial Engineering and Operations Management, 2021, pp. 363–372.
Y. T. Prasetyo and F. C. Veroya, “An Application of Overall Equipment Effectiveness (OEE) for Minimizing the Bottleneck Process in Semiconductor Industry,” in 2020 IEEE 7th International Conference on Industrial Engineering and Applications, ICIEA 2020, 2020, no. 3, pp. 345–349. doi: 10.1109/ICIEA49774.2020.9101925.
P. H. Tsarouhas, “Overall equipment effectiveness (OEE) evaluation for an automated ice cream production line: A case study,” Int. J. Product. Perform. Manag., vol. 69, no. 5, pp. 1009–1032, 2020, doi: 10.1108/IJPPM-03-2019-0126.
G. Pinto, F. J. G. Silva, A. Baptista, N. O. Fernandes, R. Casais, and C. Carvalho, “TPM implementation and maintenance strategic plan - A case study,” Procedia Manuf., vol. 51, no. 2020, pp. 1423–1430, 2020, doi: 10.1016/j.promfg.2020.10.198.
N. Sriputtha and V. Satuprapakarn, “IMPLEMENTING VALUE STREAM MAPPING AS A LEAN,” Acad. J. Manuf. Eng., vol. 19, no. 4, pp. 36–43, 2021, [Online]. Available: https://www.ajme.ro/PDF_AJME_2021_4/L6.pdf
Z. Heng, L. Aiping, X. Liyun, and G. Moroni, “Automatic estimate of OEE considering uncertainty,” Procedia CIRP, vol. 81, no. March, pp. 630–635, 2019, doi: 10.1016/j.procir.2019.03.167.
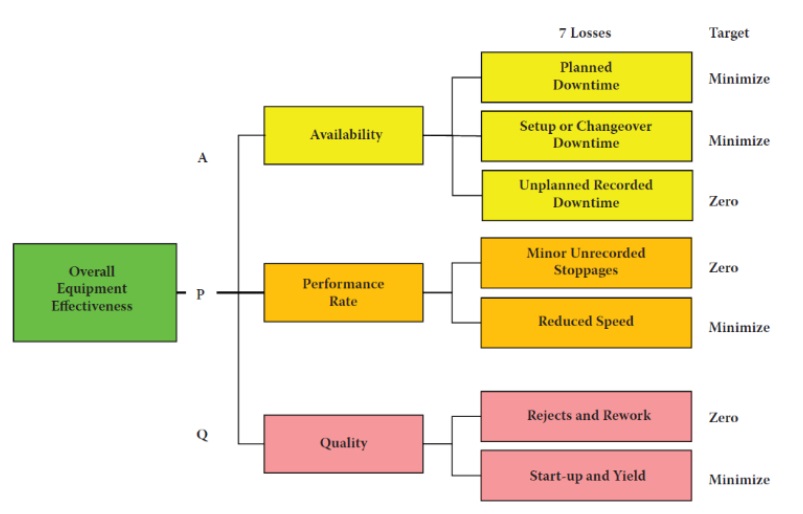
Downloads
Published
How to Cite
Issue
Section
License

This work is licensed under a Creative Commons Attribution-NonCommercial-NoDerivatives 4.0 International License.