Optimizing the Boring Parameters on CNC Machine using IS 2062 E250 Steel Plates: Taguchi-Pareto-Box Behnken Design and Taguchi-ABC-Box Behnken Design Perspectives
doi: 10.14456/mijet.2022.28
Keywords:
Box Behnken design, optimisation, signal-to-noise ratios, boring operation, surface roughnessAbstract
Due to outstanding properties such as enhanced surface roughness, fatigue strength, hardness and specific heat, the IS 2062 E250 plate has retained its competitive choice as a boring material in the automobile and aerospace industries. Unfortunately, sparse literature exists to distinguish the several boring process parameters with potential varying importance. Consequently, two novel methods are presented based on the Taguchi-Pareto-Box Behnken design (TP-BBD) and Taguchi-ABC-Box Behnken design (TABC-BBD) methods to optimize and select the process parameters. The signal to noise (SN) ratios for experimental trials was rearranged in descending order and cumulative SN ratios were computed to allow the application of the Pareto principle and the ABC methods. These outputs are fed into the Box Behnken design approach with analysis of variance conducted to reveal the linearity and significance of the parameters. Based on the process parameters considered, the response optimisation of the SN ratios for the TP-BBD method shows that the optimal setting for speed, feed, depth of cut and nose radius are 1090.91 rpm, 0.06 mm/rev, 1.2 mm, 0.606061 mm. However, for the TABC-BBD method, the response optimisation results are 800 rpm, 0.06 mm/rev, 1 mm and 0.606061 mm for speed, feed, depth of cut and nose radius, respectively. For both methods, the contour and surface plots of the SN ratios from the analysis show the range at which various parameters in the boring operation would be significant for the model.
References
G. Vohra, H.S. Sodhi & S.A. Bansal. “Prediction of optimised parameters for CNC boring process using taguchi method for steel”, International Journal of Mechanical Science and Civil Engineering, pp. 30-36, 2013.
M.P. Groover. Fundamentals of Modern Manufacturing: Materials, Processes, and Systems (4th edition ed., pp. 519-520). John Wiley & Sons, Inc., 2020.
T.T. Kumar, M. Peeraiah, S.M. Sudhan, C. Reddy. “Optimization of machining parameters of stainless steel 410 for boring operation in a lathe based on GRA”, Journal of Emerging Technologies and Innovative Research, vol. 6, no. 5, pp. 231-240, 2019b. http://dx.doi.org/10.13140/RG.2.2.19949.84967
D.P. Singh & S. Prakash. “Experimental study of taguchi vs GRA parameters during CNC boring in steel plate (SS-304)”, International Research Journal of Engineering and Technology, vol. 6, no. 8, pp. 1310-1315, 2019.
K.A. Kumar, C. Ratnam, K.V. Rao & B.S.N. Murthy. “Experimental studies of machining parameters on surface roughness, flank wear, cutting forces and work piece vibration in boring of AISI 4340 steels: Modelling and optimization approach”, SN Applied Sciences, vol. 1, no. 1, Article 26, 2019.
D. Panchal. “Optimization of surface roughness of EN-36 alloy steel on CNC turning machine using Box Behnken method under RSM”, International Journal for Research in Applied Science and Engineering Technology, vol. 8, pp. 608-625, 2020.
I.T. Abiola, S.A. Oke. “Performance evaluation of surface roughness in the boring operation of IS 2062 E250 plate on CNC machine using combined entropy-decision tree-VIKOR approach”, Indonesian Journal of Industrial Engineering & Management, vol. 2, No. 1, pp. 1-15, 2021. http://dx.doi.org/10.22441/ijiem.v2i1.10190
I.T. Abiola, S.A. Oke. “Fuzzy analytic hierarchy process and Markov-chain-WSM/WPM/WASPAS approach to solving the surface roughness problem in the boring of IS 2062 E250 steel plates on CNC machines”, Indonesian Journal of Industrial Engineering & Management, vol. 3, no. 1, pp. 47-71, 2022. http://dx.doi.org/10.22441/ijiem.v3i1.13242
P. Kumar, J.S. Oberoi, C. Singh & H. Dhiman. “Analysis and optimization of parameters affecting surface roughness in boring process”, International Journal of Advanced Mechanical Engineering , vol. 4, pp. 647–655, 2014b.
B.A. Yuvaraju & B.K. Nanda. “Prediction of vibration amplitude and surface roughness in boring operation by response surface methodology”, Materials Today: Proceedings, vol. 5, pp. 6906–6915, 2018.
K.V. Rao, B.S. Murthy & N.M. Rao. “Cutting tool condition monitoring by analyzing surface roughness, workpiece vibration and volume of metal removed for AISI 1040 steel in boring”, Measurement , vol. 46, pp. 4075–4084, 2013.
G. Schneider. “Cutting tool applications, Chapter 10: boring operations and machines-American Machinist”, Modern Machine Shop, http://www. americanmachinist. com, 2010.
K. Krishnaiah & P. Shahabudeen. Applied Design of Experiments and Taguchi Methods. PHI Learning Pvt. Ltd., New Delhi, India, 2012.
M. Patel & V. Deshpande. “Application of taguchi approach for optimization roughness for boring operation of E 250 B0 for standard IS: 2062 on CNC TC”, International Journal of Engineering Development and Research, vol. 2, no. 2, pp. 2528-2537, 2014.
W. Nugroho, N.B. Baba & A. Saptari. “Optimization on surface roughness of boring process by varying damper position”, ARPN Journal of Engineering and Applied Sciences, vol. 11, no. 20, pp. 11911-11918, 2006.
N.K. Nayak & H.S. Sodhi. “Optimization of CNC turning parameters for Al-6061 using response surface methodology”, International Journal of Mechanical and Production Engineering Research and Development , vol. 7, pp. 127–138, 2017.
V.K. Sukhdeve & S.K. Ganguly “Comparison of process parameter optimization of a jig boring process using taguchi based grey analysis and genetic algorithm”, i-Manager's Journal on Future Engineering and Technology, vol. 14, Article 58, 2019.
M. M. Abdulrazaq, A.S. Jaber, A.S. Hammood & A.G. Abdulameer. “Optimization of machining parameters for MRR and surface roughness for 7024 Al-alloy in pocket milling process”, Association of Arab Universities Journal of Engineering Sciences, vol. 26, pp. 10–16, 2019.
P.A. Kumar, C.H. Singh & H.I. Dhiman. “Analysis and optimization of parameters affecting bore deviation in boring process”, International Journal of Innovative Technology and Research, vol. 2, pp. 967–972, 2014a.
A. Abdullah, B.M. Khirulrizwan & A. Azman. “Cylindrical concentricity and coaxiality optimization for boring process by using taguchi method,” Journal of Computational and Theoretical Nanoscience, vol. 17, pp. 707–714, 2000.
D. Vivek & K. Ramesh. “Optimization of the cutting responses in boring operation using response surface methodology”, International Journal of Engineering Research, vol. 3, no. 5, pp. 1739-1744, 2014.
A. Suresh & G. Diwakar. “Investigation of effects of working parameters in turning of twip steel rods with eco-friendly cutting fluids using response surface methodology on CNC machines”, Gazi University Journal of Science, vol. 34, no. 3, pp. 68-78, 2021.
G. Balamurugamohanraj, K. Vijaiyendiran, P. Mohanaraman & V. Sugumaran. “Prediction of surface roughness based on machining condition and tool condition in boring stainless steel-304”, Indian Journal of Science and Technology, vol. 9, pp. 1–6, 2016.
M. Munawar, J.C.-S. Chen, N.A. Mufti. “Investigation of cutting parameters effect for minimization of sur face roughness in internal turning”, International Journal of Precision Engineering and Manufacturing, vol. 12, no. 1, pp. 121-127, 2011. http://dx.doi.org/10.1007/s12541-011-0015-x
G.J. Satish, H.K. Madhusudhana, B.H. Nishant & B.B. Kotturshettar. “Optimising cutting parameters in boring operation for C45 steel”, IOP Conference Series: Materials Science and Engineering, vol. 872, p. 012080, 2020.
K.V. Rao & P.B. Murthy. “Modeling and optimization of tool vibration and surface roughness in boring of steel using RSM, ANN and SVM”, Journal of Intelligent Manufacturing, vol. 29, pp. 1533–1543, 2018.
R.S. Patil & S.M. Jadhav, “Boring parameters optimization for minimum surface roughness using CNC boring machine with passive damping material”, 2017 2nd International Conference for Convergence in Technology (I2CT), pp. 300–303, 2017.
I. Ramu, P. Srinivas & K. Vekatesh. “Taguchi based grey relational analysis for optimization of machining parameters of CNC turning steel 316”, IOP Conference Series: Materials Science and Engineering, vol. 377, p. 012078, 2018.
H. Sonar, V. Saxena, V. Kshirsagar & S.P. Deshpande. “Process parameters optimization of CNC turning machine for aluminium alloy using taguchi method”, International Journal of Research in Engineering and Technology, vol. 5, pp. 36–39, 2016.
M. Thomas, Y. Beauchamp, A.Y. Youssef & J. Masounave. “Effect of tool vibrations on surface roughness during lathe dry turning process”, Computers & Industrial Engineering, vol. 31, pp. 637-644, 1996.
A. Batwara & P. Verma. “Influence of process parameters on surface roughness and material removal rate during turning in CNC lathe–an artificial neural network and surface response methodology”, International Journal of Recent Advances in Mechanical Engineering, vol. 5, no. 1, pp. 47-59, 2016.
H. Dave, L. Patel, , & H. Raval. “Effect of machining conditions on MRR and surface roughness during CNC turning of different materials using TiN coated cutting tools–A taguchi approach”, International Journal of Industrial Engineering Computations, vol. 3, pp. 925–930, 2012.
S.K. Saini & S.K. Pradhan. “Optimization of multi-objective response during CNC turning using Taguchi-fuzzy application”, Procedia Engineering , vol. 97, pp. 141–149, 2014.
Y.-K. Yang, S.-S. Lin & J.-L. Wen. “Optimization of 6061T6 CNC boring process using the taguchi method and grey relational analysis”, The Open Industrial & Manufacturing Engineering Journal, vol. 2, no. 1, pp. 14-20, 2009. http://dx.doi.org/10.2174/1874152500902010014
M. Muhammad, J.C. Chen & N.A. Mufti. “Investigation of rake angle effect for minimization of surface roughness in internal turning”, International Journal of Precision Engineering and Manufacturing, vol. 12, no. 1, pp. 121-127, 2011.
S.L.C. Ferreira, R.E. Bruns, H.S. Ferreira, G.D. Matos, J.M. David, G.E. Brandao, E.G.P. da Silva, L.A. Portugal, P.S. dos Reis, A.S. Souza, L.A. Portugal, P.S. dos Reis, A.S. Souza, W.N.L. dos Santos, “Box Behnken design: An alternative for the optimisation of analytical methods”, Analytica Chimica Acta, vol. 597, no. 2, pp. 179-186, 2007. https://doi.org/10.1016/j.aca.2007.07.011.
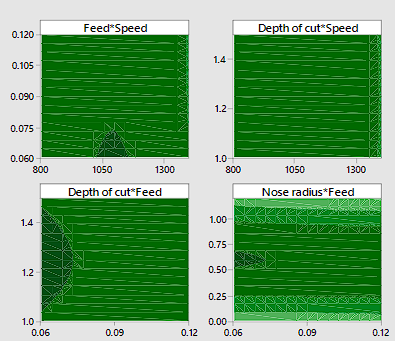
Downloads
Published
How to Cite
Issue
Section
License

This work is licensed under a Creative Commons Attribution-NonCommercial-NoDerivatives 4.0 International License.